- A+
由于涉及到氧化硅(SiO2)的连续成核和生长,用于SiO2纳米粒子合成的传统Stöber工艺通常会得到粒径大、粒径分布宽的纳米粒子。快速合成粒径分布均匀(<5%分散度)和尺寸可控的SiO2纳米粒子(20-100 nm)具有挑战性。通过原位形成瞬态胶体粒子,为SiO2的形成提供成核表面,促进SiO2的异相成核和生长有望解决这一难题。
近日,天普大学孙玉刚课题组,将聚丙烯酸(PAA)引入到由乙醇(含微量水)、正硅酸乙酯(TEOS)和氨水组成的Stöber合成溶液中,介导TEOS水解产物的成核和SiO2纳米颗粒的生长。尽管PAA和氨水单独在乙醇中都有良好的溶解性,但它们反应生成的PAA-NH3络合物在乙醇中的溶解度有限,结果形成柔性PAA-NH3复合胶体,来提供异相成核的种子促进SiO2纳米粒子的可控成核和生长,合成出粒径均匀和尺寸可控的纳米粒子。TEOS在PAA-NH3复合胶体表面水解时会产生质子,当PAA-NH3复合胶体中的NH3被质子化后,PAA-NH3络合物就会分解重新溶解于乙醇中,但这不会影响已形成的核的继续生长。
SiO2纳米粒子的数量取决于溶液中PAA-NH3复合胶体粒子的数量,PAA-NH3复合胶体粒子的形成跟PAA和氨水的摩尔比具有很强的相关性。对于同一PAA-NH3复合胶体,通过改变TEOS的量可以调节SiO2纳米粒子的尺寸。应用此方法成功地合成了直径在100 nm以下的均匀的SiO2纳米粒子(图1、2和3)。
图1. (a, b) TEM图像和(c)粒径统计图。反应物比例:5 mg PAA、1.5 mL氨水、0.75 mL TEOS和30 mL乙醇(190酒精度)。 图2. 不同PPA量合成的SiO2纳米粒子的TEM图像:(a) 0.08 g、(b) 0.01 g、(c) 0.005 g、(d) 0.002 g、(e) 0.0001 g。(f) SiO2纳米粒子的平均直径与PAA质量的线性图(误差条代表标准偏差)。 图3. (a) SiO2纳米颗粒的直径与PAA和氨水浓度的关系(误差条代表标准偏差)。(b) SiO2纳米粒子的数量(以摩尔为单位)与nPAA/nNH3·H2O的摩尔比的关系图。 图4. (a) PAA (5 mg、40 mg、80 mg)、1.5 mL氨水溶液和30 mL乙醇(190酒精度)混合物的照片。按不同的混合顺序制备:(上)序列i-PAA溶于乙醇后与氨水混合,(下)序列ii-PAA溶于氨水后与乙醇混合。(b)混合物中形成的PAA-NH3复合胶体粒子的水动力直径。 形成PAA-NH3胶粒的关键过程是PAA与氨发生酸碱反应生成在乙醇中溶解度差的PAA-NH3络合物。动态光散射(DLS)确认了PAA-NH3复合胶体的形成。PAA、氨水和乙醇可以按照两种不同的顺序混合:(i)先将PAA溶解在乙醇中,然后加入氨水(即如图1-3所示用于合成SiO2纳米颗粒的混合顺序),(ii)先将PAA溶解在氨水中,然后再与乙醇混合。当遵循混合序列i,PAA溶解在乙醇中形成透明的溶液,加入氨水后PAA浓度高的溶液变得半透明(图4a,上图),证实了PAA-NH3复合胶体的形成。DLS证实了胶体纳米粒子的形成,其流体力学直径随PAA浓度的增加而增加。按照混合顺序ii,将PAA溶解在氨水中与氨水反应生成透明的PAA-NH3络合物溶液,加入乙醇使PAA-NH3络合物聚集成胶体并呈现出半透明或乳白色的外观(图4a,下图)。 混合序列ii的观察结果表明,乙醇是PAA-NH3复合物的不良溶剂,有利于PAA-NH3胶体粒子的形成。DLS表征显示,混合序列ii形成的PAA-NH3复合胶体比混合序列i形成的PAA-NH3复合胶体大得多。由于合成溶液中PAA总量不变,混合序列ii形成的PAA-NH3复合胶体粒子数量小于混合序列i,因此,在混合序列ii的溶液中,TEOS水解产物在PAA-NH3胶粒上异相成核生长,形成粒径较大的SiO2纳米粒子(图5)。 图5. 根据混合序列ii合成SiO2纳米粒子的TEM图像,即PAA溶解在氨水中,然后与30ml乙醇(190酒精度)混合。TEOS体积为0.75 mL。(a-d) 反应溶液包含0.04 g PAA和不同量的氨水:(a) 3.0 mL、(b) 2.5 mL、(c) 2.0 mL和(d) 1.5 mL。(e, f) 反应溶液包含1.5 mL的氨水和不同质量的PAA: (e) 0.08 g和(f) 0.12 g。 论文信息 Poly(acrylic acid) Enabling the Synthesis of Highly Uniform Silica Nanoparticles of sub-100 nm Dr. Feng Hu, Dr. Kowsalya Devi Rasamani, Dr. Sasitha C. Abeyweera, Dr. Dongtang Zhang, Prof. Dr. Yugang Sun ChemNanoMat DOI: 10.1002/cnma.202200006
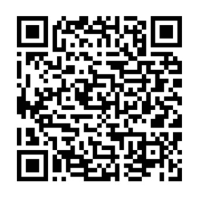
目前评论: